As you consider different options for the best method to finish your custom wrought iron project, you might wonder: what exactly is powder coating and why should I pay more for this option? Whether you’re considering a custom railing or an addition to your commercial space, a powder coating your installation will result in a durable, environmentally friendly and beautiful finish that will surely pay for itself many times over through many decades of low maintenance use. In this article we will try to explain the many benefits and answer all of your questions regarding this popular finish.
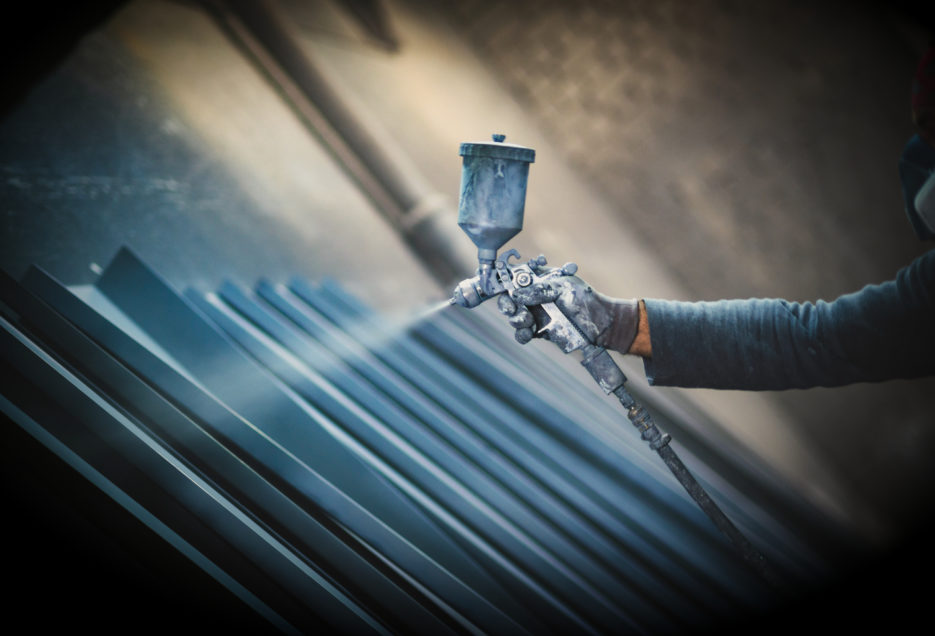
What is powder coating?
Raw metal, while flexible and beautiful, does pose a few challenges. Without a proper finish, metals exposed to the elements can tarnish, corrode and rust, drastically reducing the lifespan of the product. Metal fabricators learned long ago that a proper finish is vital to a product’s durability and longevity, not to mention that it makes the finished product look a lot better. The finished product, like a custom powder coated railing, becomes more valuable as well as more attractive, which ensures that both the fabricator and the customer end up happy with the outcome.
Paint was the finish of choice for most metal projects for many years, and while there are a lot of benefits to this option, there is some room for improvement. Brushing, rolling or spraying paint takes time and if not done correctly by a professional, the finish might not be as durable or long lasting as it could be. Another finish option is electroplating, but the chrome look is limiting and the process is both expensive and time-consuming, making it not ideal for many applications. Galvanizing is a great option for outdoor installations, but it only comes in one color and not every customer likes the industrial look of this finish. There just had to be a better option!
In 1945, Daniel Gustin invented the process of powder coating and received a US patent for his invention. This new process starts by applying a mixture of finely ground particles of pigment and resin onto a metal piece electrostatically. The charged powder adheres to the electrically grounded surface and then the piece is cured by applying heat, essentially fusing everything into a smooth coating. This results in a tougher and longer lasting finish than paint, though it took this method until 1960’s to be perfected and become popular.
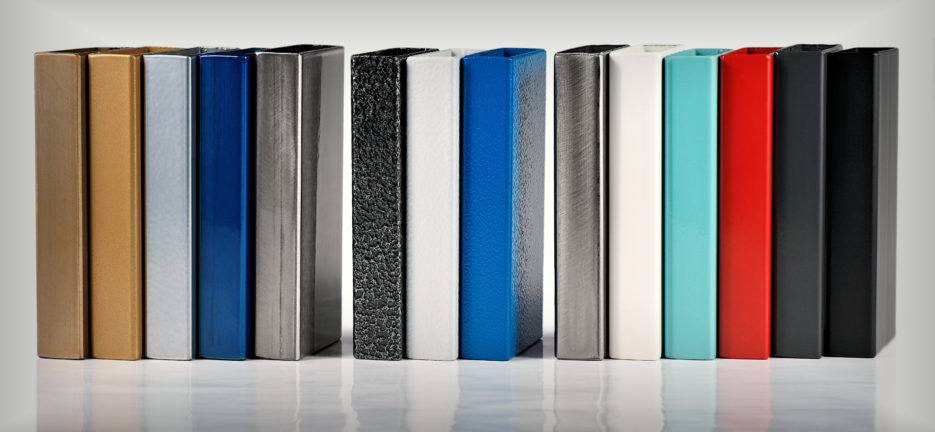
What are the benefits of powder coating?
- DURABILITY – The number one benefit of powder coating is the durability, which surpasses that of painted or plated finishes. Once the finish is cured, the powder forms chemical bonds and creates a flexible finish that is extremely resistant to corrosion, flaking, fading and scratching. The tight and even application of a powder coating allows a project to withstand extreme weather conditions, chemical contact as well as physical collision, leading to a finished product that stays vibrant and beautiful for years to come. For projects that can expect a great amount of impact or use, we can apply up to two coats as well, that way even if you were to somehow scratch the outer layer, the metal would still be amply protected from the elements. This makes it an ideal finish for a wide range of consumer goods, commercial equipment and industrial surfaces.
- UNIFORMITY – The uniformity of the finish also contributes to the beauty of the final piece. We prep all projects for powder coating by sending them out to get sand blasted first. This step, plus the nature of the powder coating process itself, ensures that the finished piece comes out smooth and uniform. There are no runs, streaks, weak spots, bubbles or dust spots in the finish, which is nearly impossible to accomplish with conventional painting, unless it’s done by a professional working in a sterile environment. A metal product with a powder coated finish, such as a custom handrail, will come out smooth and visually perfect every time.
- EFFICIENCY – There is almost no waste of material in the powder coating process due to the use of electromagnetic energy to apply the powder. This also allows an expert to apply as little or as much powder as needed for each application, getting the job done in one go instead of allowing projects to dry between coats and losing time on each curing cycle, saving the operator time and therefore money on the process. The installation process is also much quicker for powder coated pieces as there’s no on the spot welding. The pieces are simply bolted into place and that’s it.
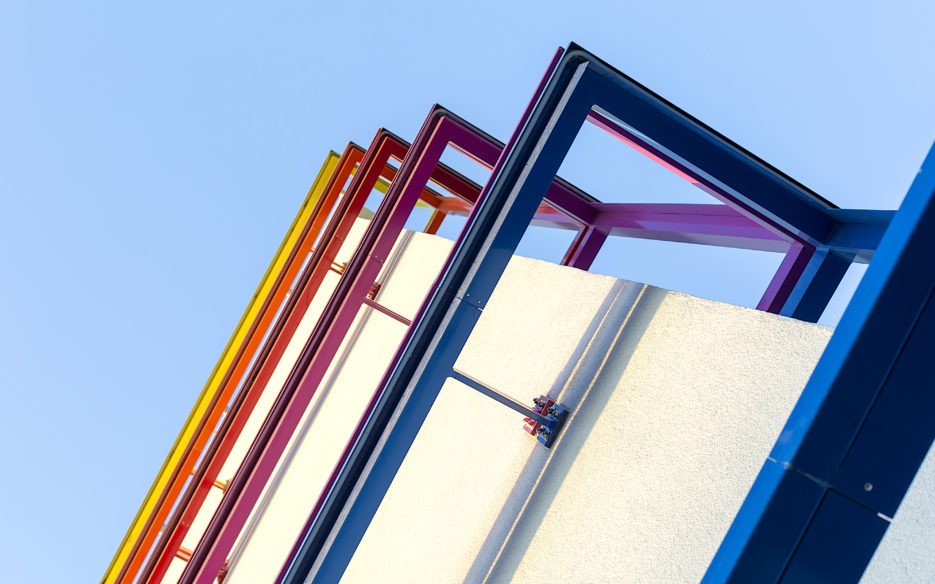
- VARIETY – There is as wide of a range of colors and textures that are available with powder coating as there are with paint, so you are not limiting your options at all by choosing this finish. The powder pigments are pre-mixed with computer controlled ratios to ensure the perfect color and color distribution, which will ensure that you get exactly what you envisioned. While black and white tend to be the most popular colors chosen for this finish, every color of the rainbow can be blended to suit any project. One of our operators can custom mix any color for the project to match your particular brand of vision.
- ENVIRONMENTALLY FRIENDLY – Powder coating also happens to be a more environmentally friendly option. Liquid finishes contain solvents which have pollutants known as volatile organic compounds (VOC’s), which are simply not part of the powder coating process. Without any toxic chemicals and solvents in its contents, the powder used in powder coating is considered to be safe for both use as well as disposal. There are no harmful chemicals released into the air and there is less waste in general involved with this process, plus there’s no need for finishers to buy and maintain costly pollution control equipment. Expert painters, however, will still ensure to take preventative measures and wear appropriate safety gear to avoid inhaling the powder and minimize skin contact.
- SAFER FOR OPERATORS – In addition to being better for the environment, this process also poses less of a threat to operators. As there are no solvents, there is a lot less irritation of the nose, mouth and throat. When painting a project, any paint that comes into contact with an operator’s skin would need to be washed off with solvent, and then removed by emulsifying with soap and hot water. Even though protective gear is still recommended when working with powder, if any does make contact with the skin, it needs nothing but some warm water to remove it.
- QUALITY – The quality of a powder coated project is hard to beat. Because of the way the powder melts and reforms as a solid, the resulting surface ends up having a smooth surface without drips or runs. This ensures that there’s no need to sand or refinish the piece if any mistakes were made.
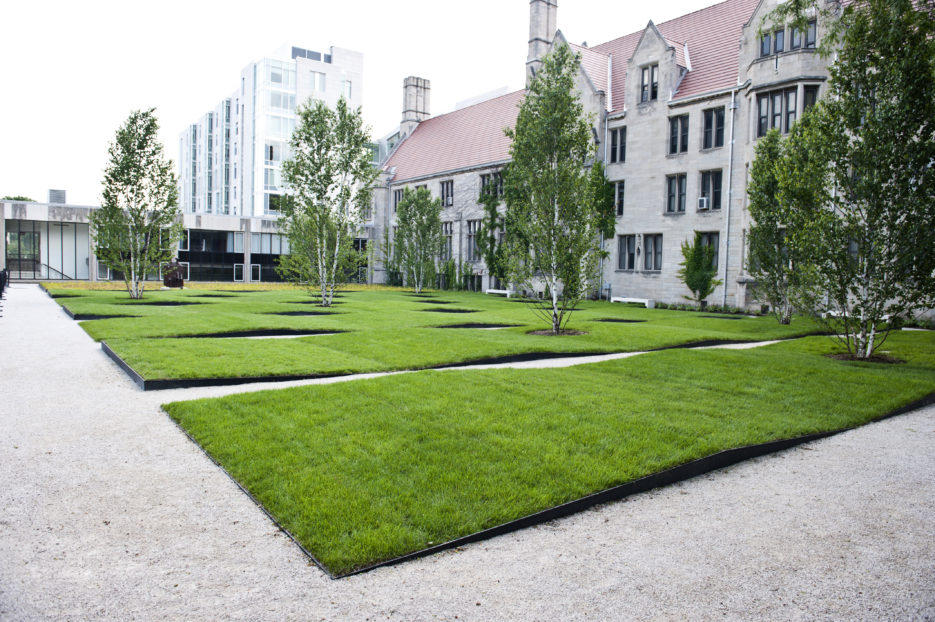
- RANGE – There is a wide range of objects that can be powder coated. If an object can take an electric charge, it can be powder coated, regardless of size, shape and intricacy of design. It’s often a challenge to evenly coat with paint irregularly shaped objects with tight bends and hollow cavities, leading to potential weaknesses in the finish and ultimately possible corrosion. This ability allows operators to evenly coat elaborate pieces in one go, without needing to paint them separately and then assembling the parts later. That said, very large pieces, such as the ones in the custom lawn edging project we did for the University of Chicago shown above, do need to be designed in such a way that they can be broken down into more manageable sections, powder coated and then assembled on site with bolts. You can’t weld a powder coated piece, so this needs to be a consideration during the design stage.
- MAINTENANCE – There are no special solvents or cleaners needed to maintain a powder coated finish. Because it is so durable, there’s no need to consider rusting or chipping when keeping your finished piece clean. In most instances all you need is the occasional pass with soapy water to keep the finished piece clean and beautiful for many years without any need for touch ups or any other maintenance work. Painted installations will need to be touched up or repainted every 5 to 10 years, but a powder coated piece will stay perfect for decades without any need of additional maintenance. This leads us to our final benefit of powder coating, it’s value.
- VALUE – A powder coated surface, such as a custom railing or a commercial awning, stands out right away to the discerning eye of a consumer, who can easily recognize the finish as one of high quality. These surfaces have a sleek and even look that is unique to this process and are guaranteed to make a bold statement in any application. Since you don’t need to maintain a powder coated installation by repainting or refinishing it, you will save yourself a lot of money over the years by avoiding the maintenance costs. A powder coated piece projects a statement of care and quality, which translates to value and satisfaction.
It’s easy to see how powder coating can make a great alternative to conventional paint finishes in many applications. With the proper equipment and procedures, powder coating decreases finishing time, improves quality and provides a wide range of finish options to the consumers. Not only is it eco-friendly and cost efficient, but your customers will also appreciate its timeless and durable finish making it well worth the investment. We do all of our powder coating work at a separate dedicated facility, so we do ask that you factor in a bit of extra time for these projects, but this option is certainly worth the wait. If you have any questions or would like to speak to one of our designers about your custom wrought iron project and our powder coating services, give us a call today!